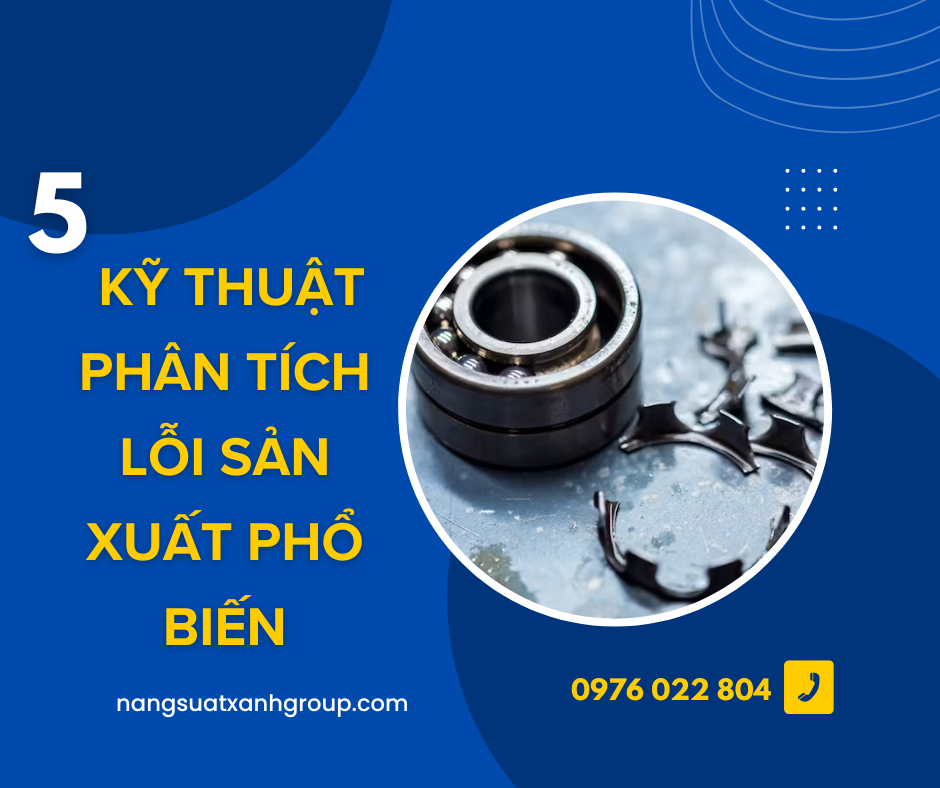
Phân tích hư hỏng giúp các nhà sản xuất khám phá nguyên nhân của các vấn đề tồn tại và ngăn ngừa rủi ro tiềm ẩn. Tiếp tục đọc để khám phá thêm, tìm hiểu về các kỹ thuật phân tích lỗi sản xuất phổ biến.
Trong môi trường sản xuất, “lỗi” đề cập đến việc mất tính liên tục trong sản xuất, do đó, có thể do thiết bị sản xuất bị lỗi hoặc các bộ phận được sản xuất sai lệch so với các thông số chất lượng đã xác định. Những thất bại này ảnh hưởng trực tiếp đến lợi nhuận của một cơ sở sản xuất và khiến công ty gặp rủi ro đáng kể.
Chúng cần được phân tích và xử lý hiệu quả để khắc phục nguyên nhân hoặc hạn chế tần suất xảy ra sự cố tiềm ẩn trong tương lai. Bài viết này sẽ mô tả một số kỹ thuật phân tích hư hỏng sản xuất thường được sử dụng.
Phân tích hư hỏng là gì?
Hầu hết các kỹ thuật Phân tích hư hỏng sản xuất đều tuân theo phương pháp cơ bản là phân tích nguyên nhân gốc rễ (RCA). Như tên gợi ý, phân tích nguyên nhân gốc rễ giúp tìm ra nguyên nhân cơ bản dẫn đến lỗi, ở cấp độ bộ phận riêng lẻ hoặc cấp độ sản xuất hàng loạt.
Ý tưởng là tiếp tục điều tra chuỗi sự kiện dẫn đến thất bại cuối cùng cho đến khi bạn tìm ra lý do cơ bản. Phân tích nguyên nhân gốc rễ giải quyết một vấn đề hiện có trong khi FMEA dự đoán các nguyên nhân gốc rễ tiềm ẩn.
Đối với sản xuất, RCA dựa trên sản xuất phát hiện ra nguyên nhân khiến các bộ phận không tuân thủ các tiêu chuẩn chất lượng hoặc thậm chí là nguyên nhân của dây chuyền sản xuất không đáng tin cậy.
Các loại phân tích lỗi sản xuất
RCA có thể được chia nhỏ thành các phương pháp phân tích hư hỏng như được mô tả bên dưới.
1. Phân tích ảnh hưởng và chế độ lỗi (FMEA)
Kỹ thuật phân tích hư hỏng sản xuất này dự đoán khả năng xảy ra lỗi tiềm ẩn, đồng thời định lượng hậu quả của chúng. Chế độ lỗi là một quá trình vật lý dẫn đến lỗi, trong khi “phân tích tác động” đề cập đến các hậu quả có khả năng phá hoại do những lỗi này gây ra.
FMEA kiểm tra vật liệu, phương pháp sản xuất, loại thiết bị được sử dụng và bất kỳ yếu tố môi trường nào có thể góp phần hoặc gây ra lỗi. Đôi khi nó được gọi là phân tích “nếu như”. Lý tưởng nhất là trước khi thực hiện một quy trình mới hoặc sản xuất một sản phẩm mới, các nhà sản xuất tiến hành FMEA.
Khi hoàn thành trong giai đoạn thiết kế/nguyên mẫu, nó giúp xác định bất kỳ rủi ro nào trước khia sản xuất và giảm rủi ro vốn có trong bất kỳ sản phẩm hoặc quy trình mới nào. Tuy nhiên, FMEA có xu hướng tốn nhiều thời gian.
2. Sơ đồ xương cá
Biểu đồ xương cá là một công cụ trực quan thể hiện bằng đồ họa các nguyên nhân gốc rễ tiềm ẩn. Hình minh họa bao gồm 2 yếu tố chính: phần đầu đại diện cho hiệu ứng hoặc sự cố và mỗi “xương” đại diện cho một loại nguyên nhân tiềm ẩn. Chúng được liệt kê như sau:
- Máy móc
- Phương pháp
- Nguyên vật liệu
- Nhân lực
- Số liệu
- Phút (thời gian).
Mỗi loại này sẽ tạo thành một xương của sơ đồ.
Sau khi được điền, sơ đồ xác định nguyên nhân gốc rễ bằng cách xác định các nguyên nhân lặp lại hoặc tần suất xuất hiện của chúng. Ngoài ra, nhóm đạt được sự đồng thuận chung về nguyên nhân gốc rễ dựa trên những hiểu biết mới thu được thông qua quy trình.
Tuy nhiên, một nhược điểm là khả năng cố gắng giải quyết mọi vấn đề được xác định thay vì những vấn đề góp phần trực tiếp vào sự thất bại cuối cùng.
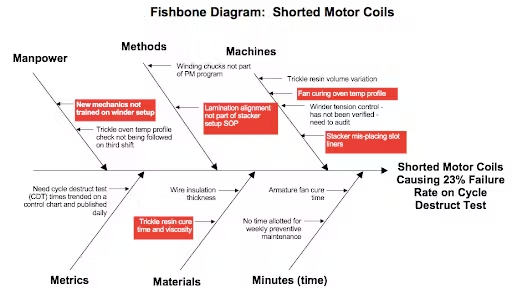
3. Cây lỗi logic
Cây lỗi logic là một kỹ thuật phân tích hư hỏng sản xuất sử dụng cấu trúc cây từ trên xuống trong đó lỗi được xác định nằm ở trên cùng của cấu trúc và các gốc cơ sở đại diện cho nguyên nhân cơ bản của lỗi.
Cây lỗi logic giúp xác định nguồn gốc vật lý, con người và tổ chức của lỗi. Các toán tử logic xác định mối quan hệ giữa các nút khác nhau trên cây, trong khi một lỗi được xác định rõ sẽ xác định tất cả các nguyên nhân tiềm ẩn.
Các lỗi được xác định kém làm chậm quá trình phân tích các nguyên nhân không quan trọng. Một xác suất xác định từng nguyên nhân trên cây. Khả năng thất bại của cây lỗi tổng thể được phân tích bằng cách sử dụng các xác suất này và các mối quan hệ được xác định trước giữa các nguyên nhân khác nhau.
4. 5 câu hỏi tại sao khi phân tích hư hỏng
Kỹ thuật phân tích hư hỏng sản xuất này là một cách đơn giản để nhanh chóng tìm ra nguyên nhân gốc rễ. Quá trình bắt đầu với một lỗi và bạn đặt câu hỏi ‘tại sao’ mỗi khi có một nguyên nhân được xác định.
Hoạt động này lặp lại cho đến khi xác định được nguyên nhân gốc rễ hoặc quá trình không kiểm soát được. Con số năm không phải là một giới hạn cứng nhắc mà là một hướng dẫn. Bạn có thể xác định nguyên nhân gốc rễ sau hai đến 10 câu hỏi tại sao, tùy thuộc vào mức độ phức tạp của vấn đề.
Việc xem xét lại thất bại từ một số quan điểm khác nhau thường giúp vạch ra các nguyên nhân. Phương pháp 5 câu hỏi tại sao không khắt khe như những phương pháp khác nhưng đôi khi có thể hiệu quả và loại bỏ được những công việc quản lý không cần thiết.
5. Phân tích dữ liệu
Với “cuộc cách mạng công nghiệp lần thứ tư” ngày càng mở rộng, các cơ sở sản xuất hiện đại có quyền truy cập ngày càng nhiều vào các tập dữ liệu phong phú với dữ liệu được thu thập từ một loạt các cảm biến IoT rẻ tiền được sử dụng để theo dõi các thông số xác định quy trình như nhiệt độ hoặc độ rung của máy.
Xác định nguyên nhân gốc rễ của dây chuyền sản xuất được phân tích thông qua dữ liệu lịch sử. Các kỹ thuật thống kê cũng được sử dụng trên các bộ dữ liệu này để dự đoán các lỗi tiềm ẩn trên thiết bị trước khi chúng gây ra sự cố tốn kém.
Phương pháp phân tích lỗi sản xuất này đang trở nên phổ biến hơn với các cảm biến rẻ hơn và các công cụ phần mềm có khả năng hơn. Các công cụ phân tích lỗi thuận tiện và giá cả phải chăng với các kỹ thuật lập mô hình quy trình thống kê đã được chứng minh cho phép các công ty tập trung vào việc phòng ngừa thông qua bảo trì phòng ngừa.
Kỹ thuật phân tích lỗi sản xuất nào là tốt nhất?
Việc quyết định sử dụng kỹ thuật phân tích lỗi sản xuất nào thường phụ thuộc vào mức độ phức tạp của lỗi, mức độ nghiêm trọng của nó và các quy trình kiểm soát chất lượng hiện có. Các phương pháp được liệt kê trong bài viết này chỉ là một phần nhỏ trong số các công cụ phân tích tiềm năng hiện có.
Thu thập dữ liệu thuần túy về lỗi thực tế giúp xu hướng phân tích dữ liệu phát triển (ví dụ: thu thập dữ liệu theo thời gian thực thay vì được thu thập từ nhiều nguồn sau đó).
Các phương pháp này cho phép các nhóm nhanh nhẹn nhỏ hơn nhanh chóng lặp lại các nguyên nhân tiềm ẩn và tìm ra nguyên nhân gốc rễ nhanh hơn so với các kỹ thuật thủ công truyền thống.
Nguồn: xometry
Bài viết liên quan:
- Một số Tip hữu ích về Kỹ thuật phân tích hư hỏng và giám sát tình trạng thiết bị
- 8 lý do để đầu tư vào giám sát tình trạng thiết bị
Hãy đăng ký ngay khóa học Kỹ thuật phân tích hư hỏng và giám sát tình trạng thiết bị” sẽ khai giảng vào ngày 15/06 để không bỏ lỡ cơ hội nâng cao kỹ năng và kiến thức của mình trong lĩnh vực Kỹ thuật phân tích hư hỏng và giám sát tình trạng thiết bị.
Xem chi tiết khoá học tại đây